Riggs Fellowship Project Examples
Project Examples
Ametek (summer 2019)
In summer 2019, we worked with Ametek on their oxygen cylinder manufacturing line. These cylinders are used for emergency overhead oxygen supply in several aircraft including the Boeing 787 and Airbus A350. The management was struggling to keep up with demand. Employees were regularly putting in 30% overtime with no relief in sight. Their scrap rate was high, and efficiency was low. Employees were tired due to working excessive over time. With the above-mentioned factors, the company’s costs were increasing, and margins were declining. Since it was a long-term contract, they had to live with the agreed upon price. Looking at the current state, we targeted a 25% reduction in their manufacturing costs. By redesigning the whole manufacturing line with lean principles, in 11 weeks (extended by a week due to holidays and conference travel) we achieved the following results.
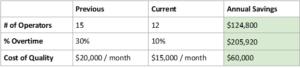
Total Annual Savings: $390,720

Monetary impact of Riggs Fellowship 2019 summer work at Ametek
As seen above, we saved the company $390,000 annually and reduced their inventory by $108,550. In addition, the non-monetary impact was a 54% reduction in lead time and a 27% increase in production. More importantly, we improved employee morale by teaching them new skills and creating an efficient work environment. We showed them a better way of manufacturing, which changed their firefighting culture to a continuous improvement culture. Ametek plans to use this new way of manufacturing companywide to increase profitability.
In achieving these results, our students worked very hard and came up with some brilliant and innovative technical solutions. They also learned soft skills such as communication, presentation, change management, and professionalism.
Recently, at the APICS fall symposium at HMC, in front of an audience of 80 people, Adam Brammer, Divisional Vice President of Ametek had the following to say about the Riggs Fellowship: “The HMC team (Riggs) work in my factory was fantastic. If your company has a chance, use them. I am planning on using them every year – because the results were amazing. I have worked with a lot of different consultants, especially on the operations side. They come in and share their ideas for improvements and present to the management and then they leave and make a bunch of money, but don’t do anything. They (Riggs team) did better than the professional consultants do. Anyway, reach out to the team.”
Adam’s statement above really sums up the impact we have made. Also, seeing the quality of work with the Riggs Fellowship at Ametek, he gave us a clinic project in the 2019-2020 year.
https://drive.google.com/file/d/1sQEHzuGWyClnc5vISCOeVhVF4NLEi3RK/view?usp=sharing
Purosil (2016-2017 academic year and summer)
In 2016, Purosil management was very frustrated with their inability to satisfy their customer demand and with the increasing costs of their Formed Hose product. Business was growing, but profitability was declining. About 60% of all orders were shipped late, which caused significant customer dissatisfaction. The management team was analyzing moving their manufacturing overseas to reduce costs. When we visited the company, it was evident that many of these problems could be easily resolved. Purosil agreed to give the Riggs Fellows an opportunity to turn the situation around.
We divided the project into two cells. In the fall of 2016 and spring of 2017 semesters, Shaan Gareeb, Alexa Le, Katherine Shim, Joe Sinopoli designed and implemented the first cell. In the summer of 2017, this team graduated, and the new team started working on the project. Ankoor Apte, Bohan Gao, Rachel Perley, and Giulia Castleberg continued with the project during the summer 2017 and completed the Lean Manufacturing implementation by designing and implementing the second cell.
The results were very impactful. Production increased from 470 products a day to 650 by the end of the summer (a 38% increase), and to 800 by October 2017 (a 70% increase). While production increased, labor costs were reduced by $518,000 annually. Due to this increased production, the company increased its revenue by 1.6 million dollars ($3.1 million if the October 2017 results are included). The backlog was reduced considerably, which allowed for a better lead-time for the customers. Late shipment was reduced from 60% to less than 5%. Their customer satisfaction improved considerably.
Here is what our students – the Riggs Fellows who worked at Purosil in summer had to say: “Thank you for allowing us this opportunity to work and make changes in a real world Gemba. All of us have learned a great deal in the course of 10 weeks. We’ve KAIZENed our knowledge as industrial engineers. Jokes aside, we all expanded our perspectives, and we are starting to see engineering as the field of making positive impact. We will apply the skills we learnt in this fellowship to all aspects of our future lives! Gambatte Kudasai!”
Mission Rubber (Summer 2015 to Summer 2019)
Vice President and General Manager of Mission Rubber, Chris Vansell is committed to working with the Riggs Fellowship in transformational projects. Mission Rubber has worked with the Riggs Fellowship for five summers. Chris Vansell stated that with tough global competition, Riggs fellowship was instrumental in keeping Mission Rubber operations in California with major cost reduction efforts.
With Chris’s encouragement and motivation, we have achieved some big successes. In 2015, we worked on process energy reduction projects. In 2016 and 2017, we worked on implementing Lean Manufacturing in their assembly operations. In 2018 and 2019, we looked at their plant holistically and strategized ideal product flow, material handling, and plant layout. This was a major step toward simplifying the whole manufacturing facility, and improving its overhead costs, safety, and supervision. Mission Rubber has spent over $200,000 on the implementation of our proposal. This optimized layout, flow, and material handling allows Mission Rubber to prepare itself for a quantum leap in modernization of its manufacturing facility. The Riggs Fellowship has played an important part in showing Mission Rubber this pathway.
After seeing the Riggs Fellowship’s impact on Mission Rubber, the company gave to us two clinic projects.