Fluidmaster Clinic: Electronic Toilet Valve to Improve Water Efficiency
January 15, 2021
Glenn Hudson ‘07 landed at Fluidmaster a few years after graduating from Harvey Mudd College, in part because he knew the company from the first Clinic project they sponsored in 2005. Fluidmaster’s original Clinic project was a great success, and the company decided to hire Joe Laubach ’05, who had been a Clinic team leader. Laubach convinced Hudson to work with him at Fluidmaster, and Hudson has now been at the company for over 10 years. Hudson had high hopes that Fluidmaster would eventually sponsor another project, and he was happy to secure resources for work on various R&D initiatives during the 2020–2021 academic year.
After discussing a few project areas with Engineering Clinic Associate Director Qimin Yang in the summer, Fluidmaster settled on a project to design an electronically controlled toilet fill valve (the valve that refills the toilet tank so the toilet can be flushed). The team’s approach has so far been to maintain much of Fluidmaster’s current design but replace the mechanical actuation and control with electronics.
“Since our project is largely design-focused, a lot of the work being done is design analysis and brainstorming,” says Jimmy Fernandez ’21, the fall project lead for the team. “The most exciting impact of the project for me is the potential water conserving features that we could explore in the valve. One of the features we are exploring is leak detection built into the valve. Leaky toilet tanks can silently waste tons of water, so any work we do to reduce this that could potentially be used on a large scale is very exciting.”
The team built two test benches at the homes of two separate team members. The test bench uses a bucket with a hole drilled at the bottom to put the fill valve through as a low-resolution replication of the toilet tank environment. Water is fed to the fill valve via a garden hose (with lots of connecting pieces).
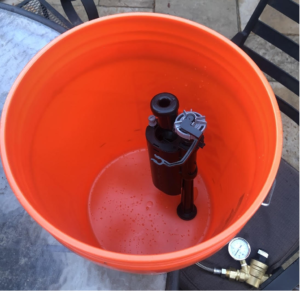
Fluidmaster Clinic team members replicated the toilet tank environment in their backyards to enable testing.
“The team has done an incredible job so far engaging with a complex topic, understanding the very strict operating requirements and regulations in the plumbing industry, and has proposed some unique solutions to the various subsystems required to make a fill valve. It’s always nice to have some fresh eyes take a look at a product from an unbiased perspective,” says Hudson. “I am also very impressed with the students’ perseverance and motivation in light of the current pandemic. There are unique challenges with remote work—limited access to resources like test labs, 3D printing and prototyping equipment—that the team has managed to overcome while maintaining productivity.”
Work during the pandemic has been a challenge, but the initial phases of the project were largely theoretical, focused on research and design. Toward the end of the fall semester, team members formulated plans to fabricate and qualify their prototypes in the spring.
“Brainstorming has been a little more difficult since it’s harder to make quick sketches of ideas,” says Fernandez. “We’ve had to experiment with different ways of effectively communicating.”