MCIE Lauds HMC Students for “Reinventing the Wheel”
February 19, 2019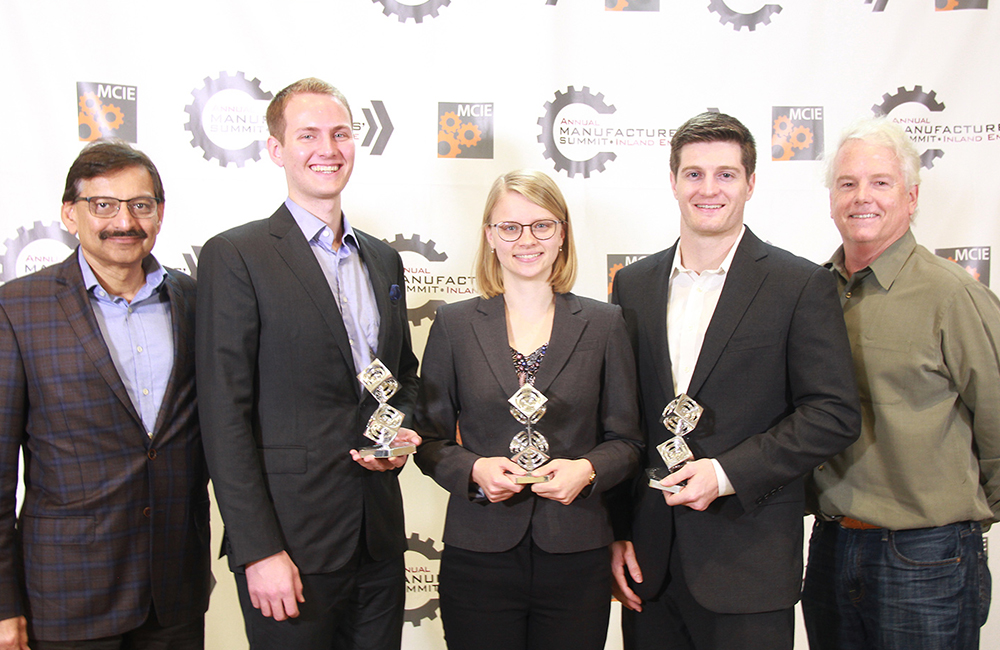
Last summer, Charles Dawson ’19, Ryan Haughton ’19 and Lydia Sylla ’19 embarked on a 10-week project to modernize manufacturing operations at Laguna Clay Company, a Los Angeles ceramic supply business. The owners of the 43-year-old company hoped to reduce clutter, streamline material handling, redesign assembly processes and improve efficiency.
The project’s success has led to recognition by the Manufacturers’ Council of the Inland Empire, which presented the students with the 2019 Innovation by Students award at the annual Manufacturers’ Summit Feb. 14. During the annual event, attendees celebrate innovative businesses and leaders who have great ideas for growing businesses, dramatically improving performance and addressing some of the toughest challenges in today’s manufacturing industry.
“We spent the first few weeks observing and understanding their processes,” says Haughton. “Overhauling an entire factory is a bit too much to do in one summer, so we piloted our improvement program in the pottery wheel manufacturing division, which was responsible for approximately 15 to 20 percent of the company’s revenue,” says Dawson.
The students named their project “Reinventing the Wheel Department” and got to work. “By the end of the 10 weeks,” says Dawson, “we had made a number of successful improvements.”
“One of the main improvements we made,” Haughton says, “was the introduction of new workstations. We designed new workstations from scratch, having locations for each tool and part the operator would need. That way, the operator would have quick access to everything they needed, reducing non-value-added time.” As a result, the students reduced the department’s lead time by 78 percent and increased output by 156 percent.
Funded by the Henry E. and Gayle Riggs Fellowship in Engineering Management, the project allowed the students to apply their classroom learning to real-world situations. “So many of the concepts and techniques we learned in E182 [Manufacturing Planning/Execution] transferred directly to the industrial setting,” Dawson says. “But, at the same time, there’s a huge difference between writing a report for a case study and actually convincing factory workers and production managers that your ideas will actually help improve operations. I gained a lot of experience working with people, leading change and communicating with/convincing the people we were working with.”
Kash Gokli, professor of manufacturing practice and Engineering Clinic director, is the team’s advisor and director of the Riggs Fellowship. “I am proud of the work our students have done as Riggs Fellows,” he says. “It is a tremendous learning experience for our students as well as a big impact on the company’s bottom line. It is a win-win.”
The students applied some “pretty solid HMC teamwork” to the process, Dawson says. “There were only three of us, and we were essentially running full-tilt for the whole summer, handing off tasks to whoever could complete them most quickly in a given moment.”
In addition to the significant lead-time reduction and increase in productivity, the team reduced the company’s work-in-process inventory by 85 percent, reduced cycle time by 50 percent on average at each assembly workstation and significantly reduced clutter in the assembly area.
“I was honestly a little bit surprised by how much of an impact we ended up having,” says Sylla. “Not only did we make it possible for them to hit their production targets, we made it possible for them to hit their production targets before lunchtime, freeing up the rest of the day for work on other projects and improvements. We also got pottery lessons while working with Laguna, which was a lot of fun.”